فهم حواجز السلامة من بيبرل فوكس للمناطق الخطرة
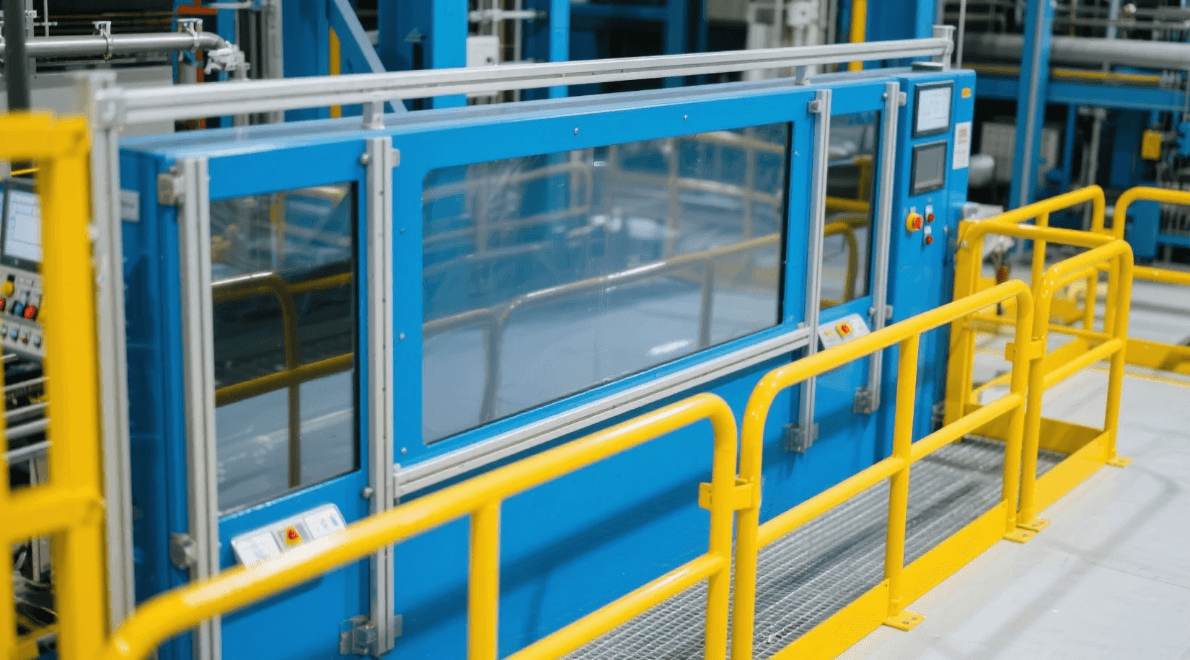
In hazardous environments, safety isn’t a luxury—it is a strict requirement. Pepperl Fuchs safety barriers for hazardous areas play a crucial role in ensuring the integrity and safety of electrical process control and automation systems. Used in industries such as oil & gas, chemicals, pharmaceuticals, and energy, these barriers protect both personnel and equipment.
What Are Safety Barriers?
Safety barriers are protective devices that limit the energy—voltage and current—that can pass into a hazardous area. Their purpose is to prevent the ignition of flammable gases or dust that could lead to explosions. In essence, they act as a safeguard between control systems and field devices located in potentially explosive atmospheres.
There are two primary types:
- Zener barriers
- Galvanic isolators
Each type has specific use cases based on system design, maintenance access, and safety requirements.
The Role of Pepperl Fuchs in Safety Solutions
Pepperl Fuchs safety barriers for hazardous areas are globally recognized for their reliability, compliance with international standards, and integration capabilities. As a pioneer in intrinsic safety and explosion protection, Pepperl+Fuchs offers a range of intrinsic safety (IS) barriers tailored to meet complex operational needs.
Key Features of Pepperl Fuchs Safety Barriers
- Intrinsic Safety (IS) Certification: Ensures that energy levels are always below ignition thresholds.
- Wide Operating Range: Compatible with a variety of sensors and actuators.
- Modular Design: Enables easy replacement and upgrades.
- Diagnostic Functions: Built-in status indicators and remote monitoring.
- Compliance: Meets ATEX, IECEx, and other regional certification standards.
These features not only enhance safety but also streamline maintenance and reduce downtime.
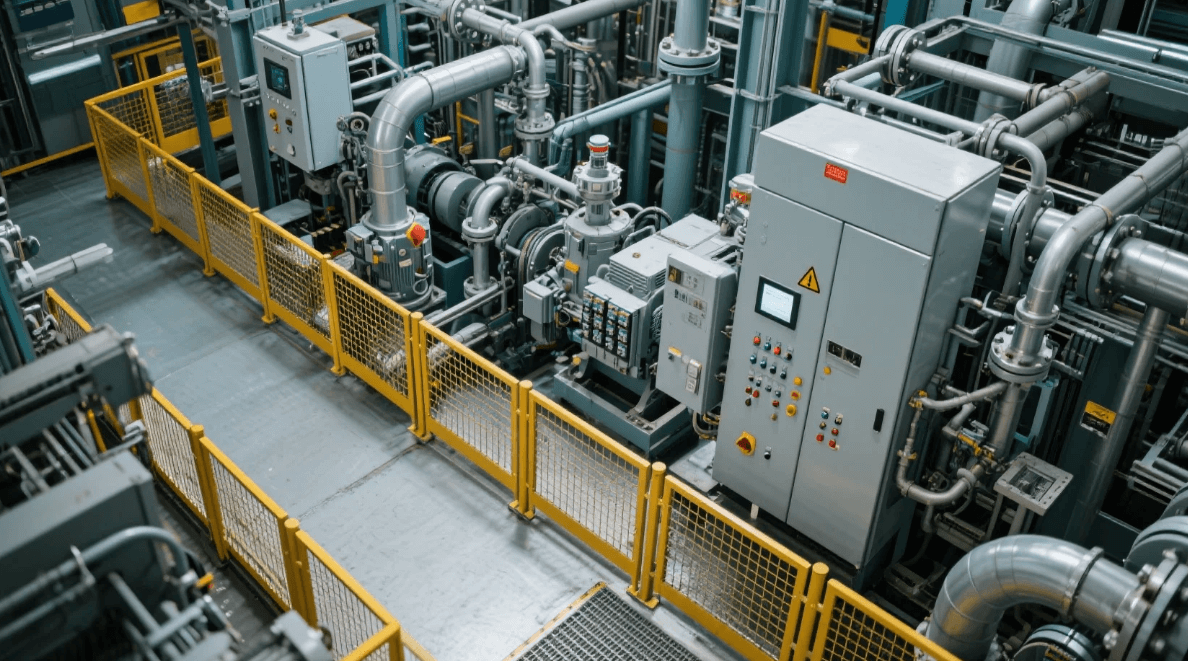
Application in Electrical Process Control and Automation
1. Signal Transmission in Hazardous Zones
In complex automation setups, process signals must be transmitted across safe and hazardous zones. Pepperl Fuchs safety barriers for hazardous areas ensure that these signals are delivered safely, without exceeding the voltage or current that could trigger an explosion.
2. Integration with DCS/PLC Systems
The barriers are easily integrated with distributed control systems (DCS) and programmable logic controllers (PLC), ensuring seamless operation and monitoring of field devices.
3. Intrinsically Safe Fieldbus Communication
Pepperl+Fuchs offers IS barriers compatible with Fieldbus Foundation and PROFIBUS-PA, enabling reliable digital communication in explosive environments.
Why Choose Pepperl Fuchs Safety Barriers?
- Engineering Expertise: With decades of R&D in explosion protection, Pepperl+Fuchs is a leader in the field.
- Wide Product Range: From simple signal converters to intelligent diagnostic barriers.
- Support and Documentation: Clear manuals, global support, and certifications.
By choosing Pepperl Fuchs safety barriers for hazardous areas, users ensure long-term safety, legal compliance, and operational continuity.
Comparing Zener and Galvanic Isolation Barriers
Feature | Zener Barriers | Galvanic Isolators |
---|---|---|
Isolation | No isolation (requires grounding) | Full galvanic isolation |
Maintenance | Simple but sensitive to ground loops | Robust and easier to maintain |
Cost | Lower upfront cost | Higher initial investment |
Signal Quality | Susceptible to interference | Superior signal integrity |
Most modern process automation users prefer galvanic isolators for their ease of use and advanced features, despite the higher cost.
Design Considerations in Hazardous Areas
When planning for barrier integration, the following factors must be evaluated:
- Zone Classification: Zone 0, 1, or 2 affects the selection of suitable barrier types.
- Device Compatibility: Barriers must match the current and voltage requirements of field devices.
- Environmental Factors: Temperature, humidity, and corrosive gases can affect barrier performance.
Designs should always comply with standards like IEC 60079 and local regulations to ensure both safety and legal compliance.
Common Industries Using Safety Barriers
- Oil & Gas: For safe monitoring of pressure, flow, and temperature.
- Chemical Processing: Ensuring explosion protection in volatile mixing environments.
- Pharmaceuticals: Safe automation in sterile and hazardous environments.
- Energy & Utilities: For control systems in high-risk transformer or battery rooms.
Each of these sectors benefits from the reliable performance of Pepperl Fuchs safety barriers for hazardous areas.
Future Trends and Innovations
Modern safety barriers are evolving to include digital diagnostics, wireless communication, and remote configuration. These innovations enhance safety while reducing manual intervention and maintenance downtime.
Pepperl+Fuchs continues to lead this evolution, with smart isolators and IIoT-ready devices entering the market.
الخاتمة
In hazardous environments where safety, compliance, and uptime are paramount, Pepperl Fuchs safety barriers for hazardous areas offer an unmatched combination of reliability, innovation, and support. By incorporating these barriers into electrical process control and automation systems, industries can achieve optimal operational safety and efficiency.
FAQs About Pepperl Fuchs Safety Barriers
Q1: What’s the difference between intrinsic safety and explosion-proof protection? A1: Intrinsic safety limits energy to prevent ignition, while explosion-proof equipment contains potential explosions.
Q2: How do I know which type of barrier to use? A2: Selection depends on application type, zone classification, and system design. Consult Pepperl+Fuchs documentation or technical support.
Q3: Are these barriers compatible with HART signals? A3: Yes, most Pepperl+Fuchs isolators support HART signal transmission.
Q4: Can safety barriers be used in Zone 0? A4: Yes, provided they are correctly rated and installed in compliance with safety standards.
Q5: How often should barriers be replaced? A5: Typically, barriers have a long lifespan but should be tested during routine maintenance, especially in harsh conditions.
Model:KCD2-STC-EX1