Phoenix Contact-Steckverbinder für die Industrieautomation: 7 wichtige Vorteile und Anwendungen
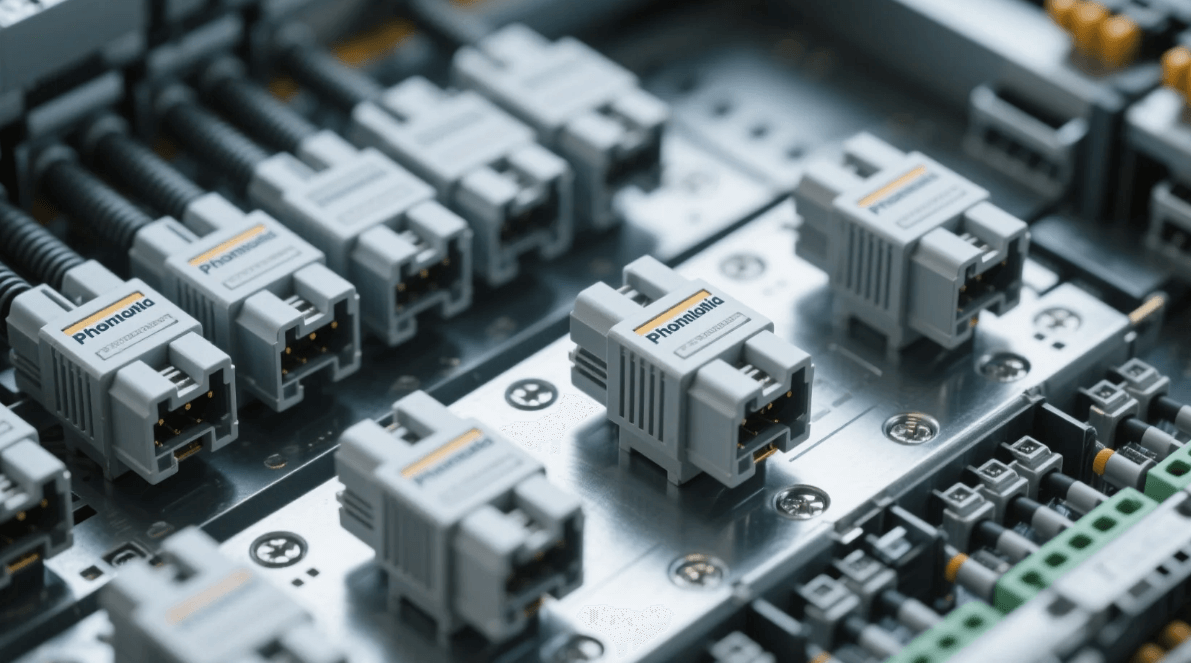
Introduction: Powering Smart Factories with Precision Connectivity
In modern Elektrische Prozesssteuerung und Automatisierung, secure and efficient connections are foundation stones of operational success. From harsh factory floors to high-speed production lines, Phoenix Contact connectors for industrial automation deliver exceptional performance and reliability. This article explains their core features, practical applications, and implementation strategies, offering valuable insights for engineers and automation specialists.
Overview of Phoenix Contact Connectors for Industrial Automation
What Sets These Connectors Apart?
Phoenix Contact has over four decades of experience in electrical interconnection technology. Their connector range addresses unique challenges in industrial environments:
- Modular Design: Components can be assembled for specific signal, power, and data requirements.
- Robust Construction: Housings resist vibration, corrosion, and extreme temperatures.
- Tool-Free Assembly Options: Quick installation without specialized tools, reducing downtime.
Product Families and Categories
Heavy-Duty Connectors (HDC)
- Rated for high current and voltage.
- Sealed to IP65/IP67 for washdown environments.
- Ideal for motor and power distribution.
Industrial Pluggable Connectors (IBC)
- Compact form factor.
- Snap-in latching systems.
- Suited for sensor and actuator wiring.
M12 and M8 Circular Connectors
- Standardized interfaces for sensors, valves, and field devices.
- Available in A-, B-, D-, and X-coding for Ethernet and fieldbus signals.
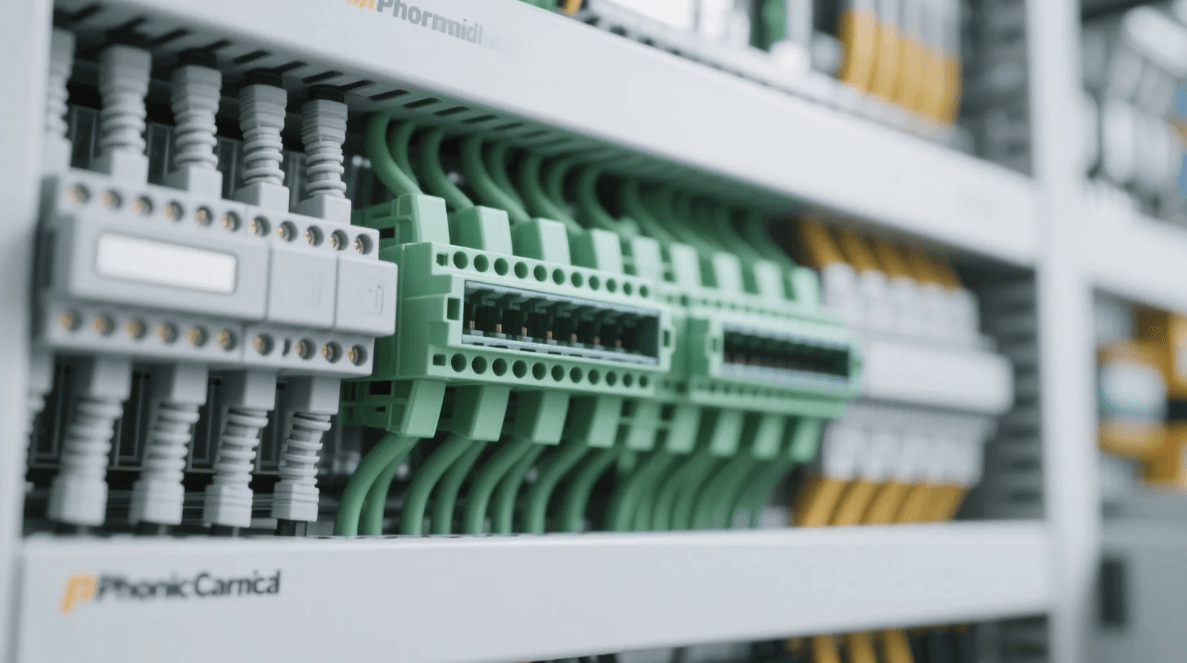
Core Features and Technical Advantages
High Durability in Harsh Conditions
Manufacturing plants often face extreme temperatures, moisture, and chemical exposure. Phoenix Contact connectors for industrial automation utilize PA, stainless steel, and TPU materials to withstand:
- Temperature ranges from -40 °C to +125 °C.
- Chemical agents in cleaning and manufacturing processes.
- Mechanical stress from vibration and shock.
Enhanced Data Transmission
As Industry 4.0 initiatives drive data-centric operations, connectors must support high-speed signals:
- Cat6A RJ45 Inserts for 10 Gbps Ethernet.
- X-Coded M12 for industrial Ethernet up to 10 Gbps.
- EMC shielding integrated to minimize electromagnetic interference.
Simplified Installation and Maintenance
Time is money in automated facilities. Phoenix Contact’s connectors feature:
- Push-in and spring-cage terminals for tool-free wiring.
- Color-coded housings to prevent wiring errors.
- Replaceable inserts that allow on-the-fly maintenance without full disassembly.
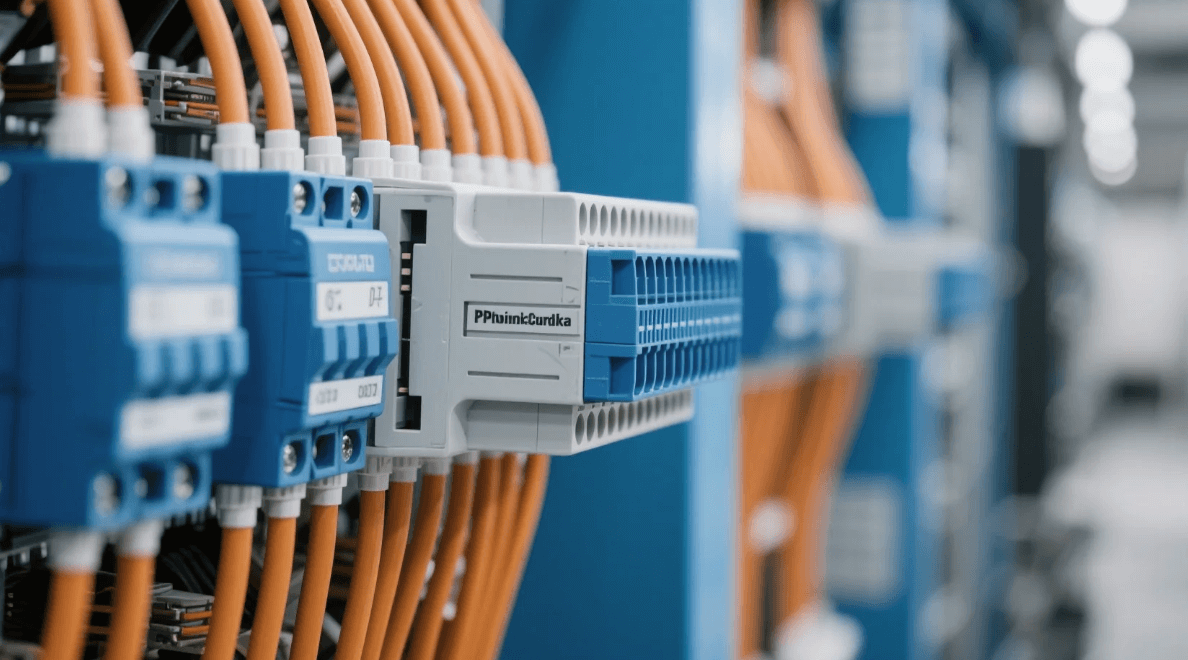
Anwendungen in der elektrischen Prozesssteuerung und Automatisierung
Machine Tool Interfacing
Precise control of CNC machines relies on high-quality connections:
- Feedback sensors for axis positions use shielded M12 connectors.
- Motor drives and power electronics integrate HDC connectors for safe energy transfer.
Distributed Control Systems (DCS)
In large-scale processing plants, distributed field I/O modules connect via pluggable connectors:
- Quick replacement of modules reduces system downtime.
- Compact footprints allow closer mounting to field devices, reducing cabling costs.
Robotics and Motion Control
Fast, reliable data links are crucial for robot coordination:
- X-Coded M12 cables maintain signal integrity for real-time control.
- Connectors rated for millions of mating cycles support daily operation.
Process Monitoring and Safety Systems
Sensors and safety relays often deploy in remote or hazardous areas:
- Explosion-proof connector variants ensure compliance with ATEX and IECEx.
- Fiber-optic connectors isolate signals in electrically sensitive zones.
Implementation Strategies for Maximum ROI
Standardization of Connector Types
By selecting a core set of connector families, organizations simplify stocking and training:
- Stock M12 A- and X-coded plugs for general I/O.
- Keep HDC variants for power modules and drives.
- Train maintenance staff on common tool-free installation procedures.
Lifecycle Management and Predictive Maintenance
Implement RFID-enabled connectors and modules to track usage history. Such digital tagging:
- Alerts technicians when mating cycles approach end-of-life.
- Enables proactive replacements, avoiding unplanned downtime.
Integration with Cable Management Systems
Organizing cables reduces installation errors and simplifies troubleshooting:
- Use Phoenix Contact’s cable ducts and labeling systems alongside connectors.
- Employ bend restrictors to maintain cable integrity under frequent movement.
Future Directions and Innovations
Miniaturization and Increased Density
As control cabinets become more crowded, demand for smaller yet robust connectors grows:
- Next-gen micro M8 connectors for compact sensor networks.
- High-density multi-pin modules supporting power and data in a single housing.
Smart Connectors and IIoT Integration
Emerging solutions embed diagnostics within connectors:
- Real-time temperature, humidity, and current monitoring.
- Cloud-based dashboards leveraging IIoT platforms to predict failures.
Sustainable and Eco-Friendly Designs
Phoenix Contact is advancing recyclable materials and energy-efficient manufacturing:
- Bioplastics in non-critical housings.
- Reduced packaging waste through modular kits.
Conclusion: Connecting Success with Phoenix Contact
Durch die Wahl Phoenix Contact connectors for industrial automation, businesses gain:
- Unmatched reliability in extreme conditions.
- Streamlined installation and maintenance.
- Future-ready data and power solutions.
Optimizing connectivity is key to achieving peak performance in Elektrische Prozesssteuerung und Automatisierung. Investing in high-quality connectors drives long-term productivity and safety.
FAQ
Q1: What is the maximum current rating for HDC connectors?
A: Heavy-Duty Connectors support up to 40 A per contact, depending on contact size and configuration.
Q2: Can Phoenix Contact connectors handle fiber-optic signals?
A: Yes, fiber-optic insert modules are available for ATEX-rated cleaning and high-voltage environments.
Q3: Are these connectors compatible with third-party cables?
A: Standardized coding (M12, RJ45) ensures interoperability, though Phoenix Contact recommends certified cables for best performance.
Q4: How does tool-free installation impact safety?
A: Reduced need for screwdrivers lowers risk of dropped tools causing shorts and speeds up secure, consistent connections.
Q5: Where can I find spare parts and accessories?
A: Phoenix Contact’s global network of distributors and online catalog provides comprehensive access to connectors, inserts, and tools.