- Allen-Bradley
- BANNER
- Bosch Rexroth
- Danfoss
- Eaton
- Festo
- Honeywell
- IFM
- Leuze
- Mitsubishi
- MTL
- Nidec
- Omron
- FUCILI DI PEPPERL
- Modulo diagnostico avanzato
- Cavo di collegamento
- Codificatore
- Barriera bus di campo
- Multiplexer HART
- Sensore di inclinazione
- Sensore induttivo
- Unità di valutazione RFID
- Scheda di terminazione
- Sensore a ultrasuoni
- Attuatori per valvole
- Barriera di sicurezza e isolatore
- Barriera di protezione contro le sovratensioni
- Contatto Phoenix
- PILZ
- PULS
- SICK
- Siemens
- Schneider
- Turck
- Wago
- Yokogawa
Industrial Networking: The Backbone of Modern Electrical Systems

Introduction: The Critical Role of Industrial Networking in Electrical Infrastructure
In the ever-evolving electrical industry, digitalization and automation have redefined how systems communicate, operate, and scale. At the core of this transformation lies Industrial Networking, which enables robust, secure, and high-speed data exchange between industrial devices and control systems. Its role has grown from optional integration to indispensable infrastructure for manufacturers, utilities, and OEMs seeking efficiency, transparency, and predictive capabilities.
What Is Industrial Networking?
Industrial Networking refers to the communication systems used to connect devices, machinery, and control platforms within an industrial environment. Unlike traditional IT networks, these networks are engineered for rugged conditions, deterministic data transmission, real-time performance, and fail-safe operations.
These networks form the backbone for SCADA, DCS, PLCs, RTUs, and smart sensors to coordinate and execute complex operations. They utilize specialized protocols such as PROFINET, EtherNet/IP, Modbus TCP, and OPC UA to ensure interoperability and real-time responsiveness.
Key Features of Industrial Networking

Deterministic Communication
Ensures predictable and guaranteed data delivery—essential for time-critical industrial processes.
High Availability and Redundancy
Networks are designed with failover mechanisms like ring topologies and dual-homing to prevent downtime.
Real-Time Data Acquisition
Continuous data from sensors and actuators supports monitoring, diagnostics, and control in milliseconds.
Environmental Ruggedness
Components are built to operate in extreme temperatures, humidity, and vibration common in electrical substations and industrial floors.
Security Built for Industry
Incorporates industrial-grade firewalls, access control lists (ACLs), and intrusion prevention to protect against cyber threats.
Advantages of Using Industrial Networking in the Electrical Industry
Increased Operational Efficiency
Automated coordination among devices minimizes manual intervention and reduces human error.
Predictive Maintenance and Downtime Reduction
By analyzing networked device data, maintenance can be planned proactively, avoiding costly breakdowns.
Scalability for Future Expansion
Industrial networks are modular, allowing seamless integration of new devices and systems without major infrastructure changes.
Data Transparency and Analysis
Real-time and historical data enable informed decisions for load balancing, energy management, and process optimization.
Sicurezza migliorata
Continuous monitoring of electrical systems enables rapid detection of faults and implementation of safety shutdowns.
Typical Applications in the Electrical Sector
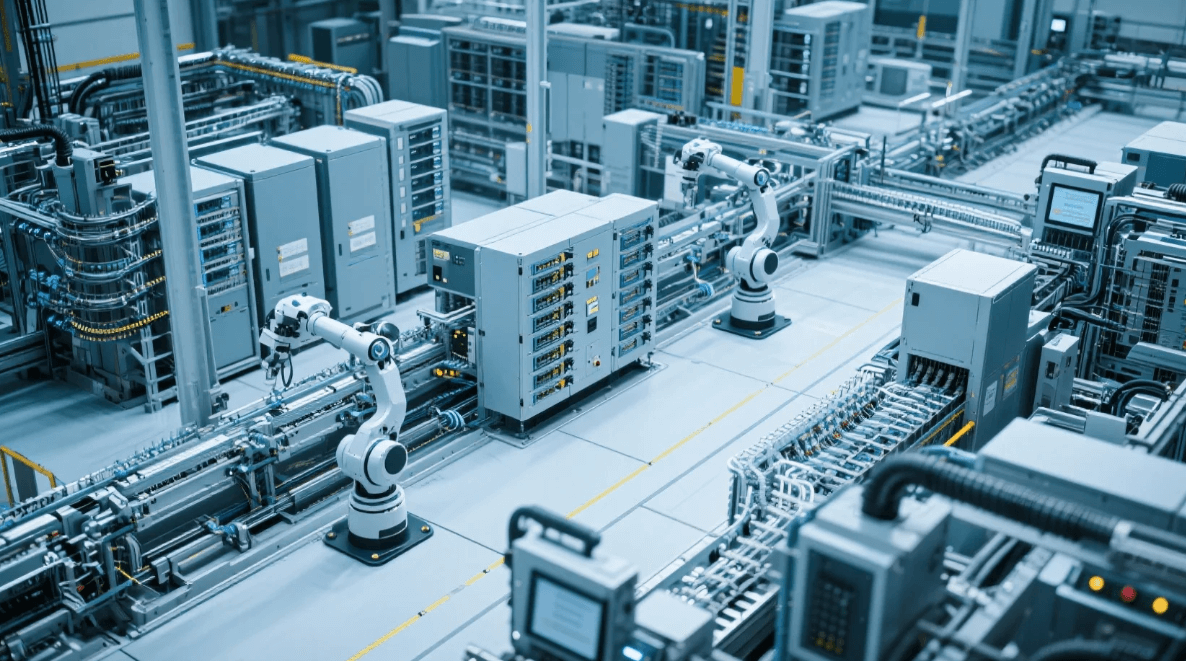
- Substation Automation: Enables IEC 61850-based control and monitoring of transformers and switchgear.
- Industrial Control Panels: Networking ensures centralized PLC communication with I/O modules and drives.
- Smart Grid Management: Facilitates two-way communication between energy producers and consumers.
- Sistemi di monitoraggio remoto: Allow operators to access equipment status, alarms, and logs from anywhere.
- Building Automation: Integrates HVAC, lighting, and power systems for energy-efficient operations.
Key Industrial Networking Protocols
- PROFINET: Used for real-time communication in automation applications.
- EtherNet/IP: Integrates with Rockwell and Allen-Bradley systems for factory-level control.
- Modbus TCP/IP: A widely adopted protocol for simple, cost-effective device communication.
- OPC UA: Offers platform-independent interoperability and strong security features.
- IEC 61850: Specifically designed for electrical utility automation systems.
Factors to Consider When Designing an Industrial Network
- Topology Selection: Choose between star, ring, bus, or mesh depending on system complexity and redundancy needs.
- Latency Requirements: Ensure the chosen protocol meets response time targets for your application.
- Bandwidth and Traffic Load: Match switch and router capacities with expected data flow.
- EMI/EMC Considerations: Shielding and grounding become critical in high-voltage environments.
- Scalability and Integration: Plan for future technology upgrades, including IoT and edge computing.
Integration with Industry 4.0 and IIoT
The integration of Industrial Networking with Industry 4.0 initiatives enables:
- Predictive analytics using AI-driven data insights.
- Decentralized control via edge computing.
- Real-time collaboration across global production sites.
- Smart sensors reporting health and efficiency of devices in real-time.
Security Challenges and Solutions in Industrial Networks
Threat Landscape
From ransomware to unauthorized access, industrial networks are increasingly targeted by sophisticated cyberattacks.
Recommended Security Practices
- Use VLANs to segment traffic.
- Implement network access control (NAC).
- Deploy firewalls and IDS/IPS systems.
- Update firmware regularly and enforce strong authentication.
Real-World Example: Industrial Networking in Power Distribution
In a large-scale power distribution facility, Industrial Networking enabled seamless communication between circuit breakers, protective relays, and monitoring systems. This setup reduced manual intervention, provided real-time fault isolation, and improved grid stability. Maintenance response times dropped by over 40% due to automated fault detection and notification systems.
Prospettive future per Industrial Networking
As the demand for electrification, automation, and smart energy management grows, Industrial Networking will evolve with:
- 5G-enabled industrial devices.
- Time-Sensitive Networking (TSN) for synchronized, high-bandwidth applications.
- Cybersecure, AI-enhanced automation platforms.
- Integration with digital twins and augmented reality for maintenance and training.
Final Thoughts: Why Industrial Networking Is a Strategic Investment for Electrical Systems
In an industry where uptime, efficiency, and safety are paramount, Industrial Networking is not merely a communication layer—it is the nervous system of modern electrical infrastructure. Companies investing in robust, scalable, and secure networking systems are better positioned to innovate, adapt, and lead in a rapidly changing technological landscape.
FAQs – Industrial Networking
Q1: What is the main difference between industrial and IT networks?
A1: Industrial networks are optimized for real-time control, environmental toughness, and deterministic behavior, unlike general IT networks.
Q2: Is Industrial Networking only used in factories?
A2: No, it’s also critical in power grids, smart buildings, and transportation systems.
Q3: How can I secure an industrial network?
A3: Use segmentation, firewalls, access controls, and encrypted communication protocols.
Q4: Can legacy equipment be integrated into an industrial network?
A4: Yes, using protocol converters and gateways, older devices can communicate with modern networks.
Q5: What’s the biggest challenge in deploying Industrial Networking?
A5: Balancing performance, reliability, and security while integrating heterogeneous devices across legacy and new infrastructure.