Vision Systems: The Eyes of Industrial Innovation

Introduction: Seeing the Future Through Automation
In today’s data-driven manufacturing landscape, Vision Systems are redefining precision and productivity. More than just cameras, these intelligent systems leverage sensors, software, and AI to inspect, analyze, and guide machinery across industrial applications. As electrical sector enterprises embrace automation, vision technology plays a pivotal role in quality assurance, predictive maintenance, and safety compliance.
What Are Vision Systems?
Vision Systems are computer-based solutions equipped with high-resolution sensors and image processing software. These systems perform tasks such as:
- Detecting defects in components
- Guiding robotic arms with millimeter accuracy
- Reading barcodes and QR codes
- Monitoring production lines in real-time
Whether on the factory floor or in electrical substations, their deployment streamlines operations and reduces human error.
Key Benefits of Vision Systems in Electrical Applications
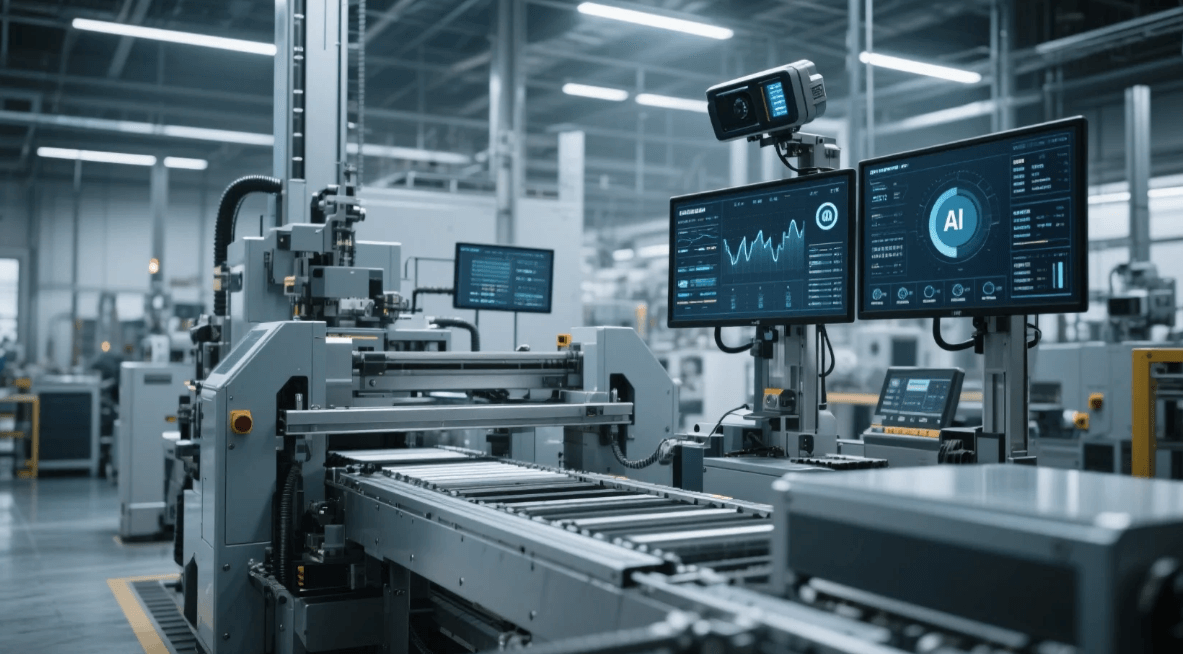
1. Precision Quality Control
Electrical components demand ultra-high accuracy. Vision systems instantly detect flaws like soldering issues, cracks, or alignment defects, ensuring only compliant units pass inspection.
2. Enhanced Operational Efficiency
These systems operate 24/7, reducing downtime and eliminating bottlenecks that arise from manual inspection.
3. Safety and Compliance
By monitoring worker behavior and verifying PPE usage, vision systems contribute to a safer and regulation-compliant workspace.
4. Real-Time Data Analytics
Image data processed by AI offers actionable insights. Electrical manufacturers can adapt instantly to production anomalies or predict failures.
Common Applications Across the Electrical Sector
- PCB (Printed Circuit Board) Inspection
- Assembly line monitoring
- Smart energy meter verification
- Robotic process guidance
Vision Systems vs. Manual Inspection
Feature | Vision Systems | Manual Inspection |
---|---|---|
Speed | Ultra-fast (ms) | Slow and subjective |
Accuracy | >99% | Variable |
Consistency | Always uniform | Depends on human factors |
Data Capture | Automated & stored | Rarely documented |
Cost (Long-Term) | Lower with scale | Higher over time |
The contrast highlights why automation using Vision Systems is the preferred route for scaling precision.
Implementing Vision Technology in Electrical Infrastructure
1. Define Application Scope
Is it for inspection, measurement, or process control? Defining goals helps select the right hardware and software.
2. Choose the Right Sensors
From line-scan cameras to 3D vision, each application demands tailored sensor capability.
3. Integrate With Control Systems
Vision units should communicate seamlessly with PLCs or SCADA for automation workflows.
4. Training and Support
Operator training ensures the full value of implementation is realized.
Economic and Environmental Impact
- Waste Reduction: Faulty units are detected early, reducing scrap.
- Efficienza energetica: Automated systems optimize power usage.
- Operational Cost Saving: Less labor-intensive and more consistent.
Overcoming Implementation Challenges
1. Initial Setup Investment
Solution: Begin with high-ROI areas and scale gradually.
2. Lighting and Environment Control
Solution: Use infrared or structured lighting to overcome ambient light issues.
3. Data Overload
Solution: Implement AI-based filtering to prioritize critical alerts.
Vision Systems and Industry 4.0
The evolution of Vision Systems aligns with the rise of smart factories. Key trends include:
- AI and deep learning algorithms for defect classification
- Edge computing for low-latency processing
- Cloud-based vision analytics for remote monitoring
Conclusion: Vision Systems as Strategic Assets
For the electrical industry, adopting Vision Systems means far more than automating inspections. It represents a strategic investment in quality, agility, and sustainability. As technologies advance, these systems will become the standard eyes and brains of the smart industrial ecosystem.
Domande frequenti
1. Can Vision Systems work in low-light environments?
Yes, specialized lighting and infrared sensors are designed for such conditions.
2. Are they suitable for high-speed assembly lines?
Absolutely. Most modern systems are capable of inspecting thousands of units per minute.
3. How long does implementation typically take?
From planning to deployment, 2 to 6 weeks depending on scale.
4. Do Vision Systems require regular calibration?
Yes, periodic calibration ensures sustained accuracy.
5. Can they be integrated with AI analytics?
Definitely. AI integration is now common for defect detection, classification, and predictive maintenance.