How to Choose the Right Sensor for My Industrial Application
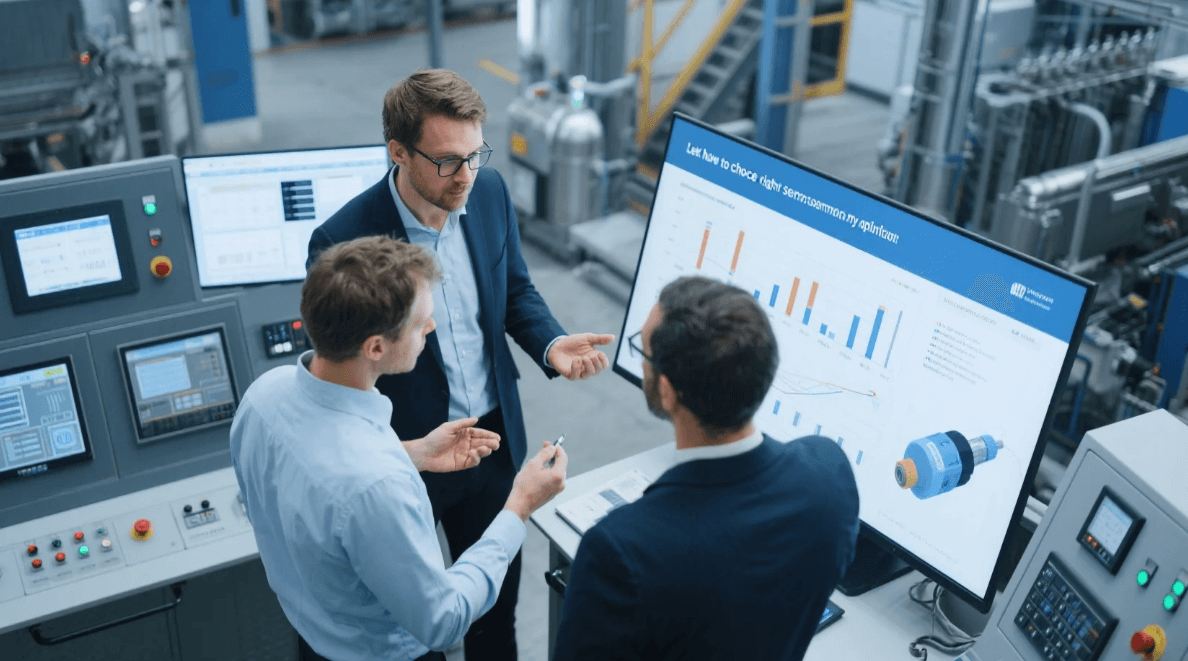
はじめに
Choosing the correct sensing technology can make or break an automation project. In this guide, how to choose the right sensor for my industrial application is explored in depth. Within the electrical process control and automation field, sensors provide critical feedback for maintaining process stability, ensuring safety, and achieving peak performance. By understanding key factors—such as measurement requirements, environmental conditions, and integration needs—you will be equipped to select sensors that deliver reliable, long-term value.
Why Sensor Selection Matters
In electrical process control and automation, a sensor’s role is foundational. It transforms physical phenomena into signals that controllers interpret. When the selection is guided by clear criteria, processes remain stable—downtime is reduced, and product quality remains high. Conversely, inappropriate choices can lead to inaccurate readings, frequent replacements, and costly overruns.
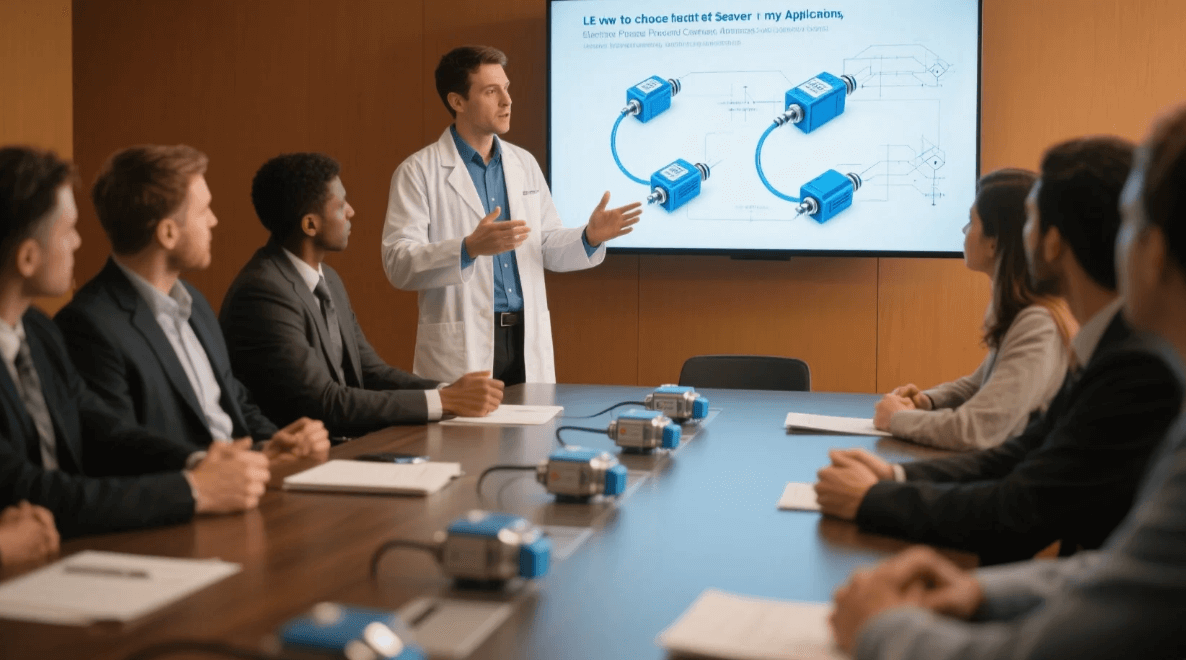
Key Considerations
Choosing how to choose the right sensor for my industrial application hinges on several interrelated factors:
Measurement Parameters
- Physical Variable: Identify whether you need to measure temperature, pressure, flow, level, proximity, or another variable.
- Range and Span: Ensure the sensor’s measurement range covers the minimum and maximum expected values.
- Response Time: Faster response is crucial for dynamic processes, whereas slower processes may tolerate a higher response latency.
Environmental Conditions
- Temperature Extremes: High or low ambient temperatures can affect sensor longevity.
- Humidity and Corrosives: Sensors exposed to moisture or chemicals must have appropriate ingress protection (e.g., IP67 or higher).
- Vibration and Shock: Robust housing and mounting are essential in high-vibration environments.
Signal and Communication Needs
- Analog vs. Digital: Decide between 4–20 mA, 0–10 V, HART, Modbus, or IO-Link based on existing PLC/DCS compatibility.
- Wiring Distance: For long runs, current loops (4–20 mA) often outperform voltage signals.
- Wireless Options: When wiring is impractical, wireless sensors can offer flexibility, though they may introduce latency and require battery maintenance.
Accuracy, Precision, and Resolution
- Accuracy: Maximum allowable error relative to true value (e.g., ±0.5 °C).
- Precision/Repeatability: Consistency of readings under identical conditions.
- Resolution: Smallest change detectable; critical when fine control is required.
Durability and Maintenance
- Mean Time Between Failures (MTBF): Longer MTBF reduces unplanned maintenance.
- Calibration Requirements: Some sensors demand frequent recalibration, adding to operational costs.
- Self-Diagnostics: Modern sensors with onboard diagnostics can alert when performance drifts.
Compliance and Safety Standards
- Industry Regulations: Food, pharmaceutical, and chemical sectors often require FDA, ATEX, or SIL certifications.
- Explosion-Proofing: For hazardous areas, choose sensors rated for the specific zone classification.
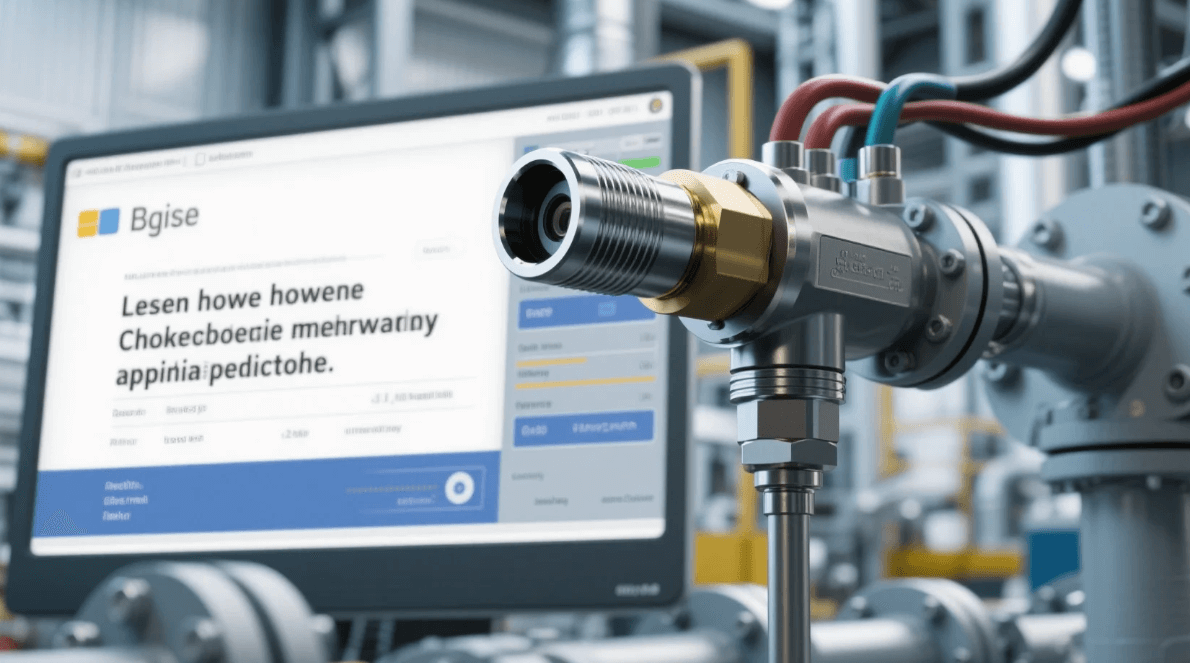
Sensor Types Overview
Temperature Sensors
- Thermocouples: Rugged and wide-range, but require cold-junction compensation.
- RTDs (Resistance Temperature Detectors): High accuracy and stability, albeit more expensive.
- Infrared Sensors: Non-contact measurement; useful for moving parts or toxic materials.
Pressure Sensors
- Diaphragm-Based: Suitable for liquids and gases; available in absolute, gauge, and differential types.
- Piezoresistive: High sensitivity; often used in hydraulic and pneumatic systems.
Flow and Level Sensors
- Ultrasonic and Radar: Non-intrusive, ideal for corrosive or sanitary fluids.
- Magnetic and Vortex: Rugged options for conductive liquids or steam flow measurement.
Proximity and Position Sensors
- Inductive: Detect metal objects without contact.
- Capacitive: Sense a wide range of materials, including plastics and liquids.
- Photoelectric: Versatile but susceptible to dust or moisture interference.
Vibration and Condition Monitoring
- Accelerometers: Monitor bearing health; predictive maintenance relies heavily on vibration data.
- Ultrasonic Leak Detectors: Identify compressed air leaks, steam traps failures, and electrical discharges.
Step-by-Step Selection Process
- Define the Application Requirements
- Specify measurement type, range, and environmental constraints.
- Shortlist Sensor Technologies
- Compare broad families (e.g., thermocouple vs. RTD).
- Evaluate Integration
- Check compatibility with PLC/DCS, communication protocols, and power requirements.
- Assess Total Cost of Ownership
- Factor in purchase price, installation, calibration, and maintenance.
- Request Samples and Field Test
- Whenever possible, perform on-site trials to verify performance.
- Finalize and Document
- Record calibration certificates, wiring diagrams, and operating manuals.
Real-World Examples
- Chemical Reactor Temperature Control: An RTD was chosen over a thermocouple for its superior stability, ensuring consistent product quality over thousands of cycles.
- High-Pressure Hydraulic System: A piezoresistive pressure sensor with explosion-proof housing met both measurement and safety needs.
- Remote Tank Level Monitoring: A radar level sensor communicated wirelessly to a cloud-based SCADA system, eliminating costly cable runs.
Integration Best Practices
- Proper Mounting: Use vibration-damping brackets where necessary.
- Shielded Cabling: Prevent electrical noise from corrupting low-level signals.
- Grounding and Bonding: Avoid ground loops by following manufacturer guidelines.
- Periodic Calibration: Schedule recalibration in maintenance plans to ensure continuous accuracy.
Common Pitfalls to Avoid
- Ignoring Environmental Factors: A sensor rated for indoor use may fail in outdoor or corrosive settings.
- Over-Specifying Accuracy: Higher accuracy often comes at disproportionate cost; match spec to actual needs.
- Neglecting Signal Integrity: Long analog runs without proper wiring can lead to drift and noise.
- Underestimating Maintenance: Skip specifying recalibration intervals, and sensor performance may degrade unnoticed.
Future Trends
- Smart Sensors: With embedded AI/ML, sensors will adapt calibration curves in real time.
- Edge Computing: Processing data locally within the sensor reduces network load and latency.
- Digital Twins: Virtual replicas of processes will rely on high-fidelity sensor data for simulation and optimization.
よくあるご質問
Q1: What is the first step in selecting an industrial sensor?
The initial step is defining your measurement requirements: parameter type, range, accuracy, and environmental conditions.
Q2: Can I use a generic sensor for multiple applications?
While tempting, generic sensors often lack the specialized features needed for critical control tasks, leading to compromised performance.
Q3: How often should sensors be calibrated?
Calibration intervals depend on sensor type and usage but are commonly set between six to twelve months.
Q4: Are wireless sensors reliable in industrial settings?
Modern wireless sensors with industrial protocols (e.g., WirelessHART) are reliable, but network planning and interference analysis remain essential.
Q5: Do smart sensors eliminate the need for calibration?
Smart sensors can self-diagnose drift but still require periodic calibration to maintain traceability and regulatory compliance.
By following this comprehensive framework on how to choose the right sensor for my industrial application, engineers and automation professionals can make informed decisions that enhance reliability, safety, and efficiency within electrical process control systems.