IFM Condition Monitoring: Revolutionizing the Electrical Industry with Smart Monitoring Solutions
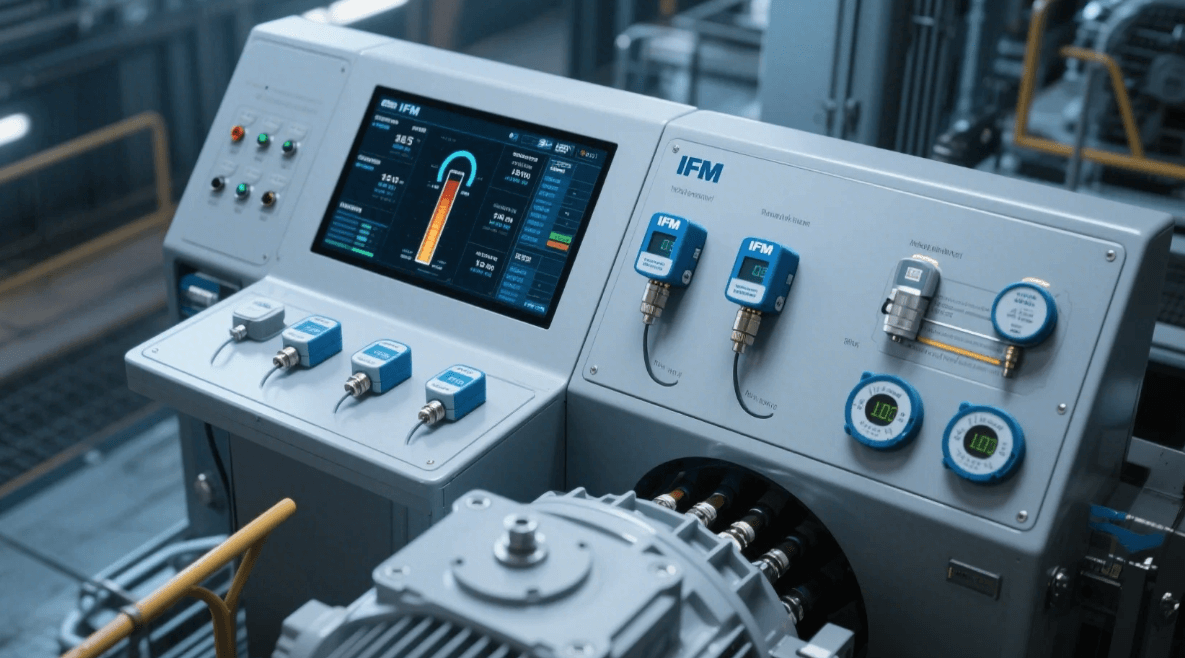
In the rapidly evolving electrical industry, Condition Monitoring has become an essential tool for businesses aiming to maximize operational efficiency, reduce downtime, and increase equipment lifespan. Condition Monitoring refers to the process of continuously assessing the health and performance of electrical equipment, machinery, and systems. With the advent of cutting-edge technology, companies like IFM have developed advanced monitoring solutions that help businesses predict and prevent equipment failures before they occur.
The Growing Need for Condition Monitoring in the Electrical Industry
Proactive Maintenance Over Reactive Repair
In the past, many companies operated under a reactive maintenance strategy—waiting for equipment to fail before addressing issues. However, with the implementation of Condition Monitoring, electrical companies can now take a proactive approach. Instead of reacting to failures, businesses can continuously monitor the condition of their equipment, predict potential issues, and schedule maintenance when needed, avoiding costly breakdowns and unplanned downtime.
The Role of IFM in Condition Monitoring
IFM, a leading provider of industrial automation solutions, has played a crucial role in advancing Condition Monitoring technologies. Their smart sensors and monitoring systems provide real-time data on the health of electrical components, allowing for precise analysis and timely interventions. These solutions have proven to be a game-changer for electrical businesses, significantly improving efficiency and cost-effectiveness.
Key Advantages of Condition Monitoring in the Electrical Industry

1. Improved Equipment Reliability
の最も重要な利点のひとつは、その品質である。 Condition Monitoring is the ability to improve equipment reliability. By continuously monitoring the condition of machinery, electrical businesses can detect early signs of wear and tear, preventing catastrophic failures. This leads to fewer unplanned downtime events and better overall performance.
IFM’s condition monitoring systems, which include vibration sensors, temperature sensors, and pressure monitoring tools, ensure that every component is operating within the desired parameters. If a deviation is detected, an alert is triggered, enabling quick action before a failure occurs.
2. Cost Savings through Predictive Maintenance
The implementation of Condition Monitoring can lead to substantial cost savings. Traditional maintenance strategies, such as scheduled maintenance or reactive repair, can result in unnecessary downtime or expensive emergency repairs. In contrast, predictive maintenance—which is made possible through real-time data provided by condition monitoring—allows businesses to address issues only when they arise.
By catching problems early, companies can avoid the significant costs associated with complete system failure. Additionally, this approach extends the lifespan of equipment, further reducing replacement and repair costs over time.
3. 効率と生産性の向上
With Condition Monitoring, electrical companies can optimize the performance of their equipment. By continuously collecting data, businesses can gain a deeper understanding of their equipment’s performance, allowing them to fine-tune operations. This leads to higher efficiency and increased productivity, as machines run at optimal performance levels, without the need for constant adjustments or frequent repairs.
4. Minimized Downtime and Increased Operational Availability
Downtime is one of the biggest challenges facing electrical companies, as it disrupts operations, reduces output, and leads to financial losses. Through Condition Monitoring, downtime can be minimized by detecting problems before they result in complete failures. IFM’s monitoring systems allow for early detection of issues, enabling businesses to take proactive measures such as rescheduling operations or performing targeted maintenance during off-peak hours.
5. Enhanced Safety and Risk Management
In the electrical industry, safety is of utmost importance. Condition Monitoring plays a critical role in preventing hazardous situations, such as electrical fires or power surges. By constantly tracking the health of electrical equipment, businesses can identify potential risks early and mitigate them before they escalate into dangerous situations.
For instance, temperature sensors used in Condition Monitoring can detect overheating issues in electrical systems, which could potentially lead to fires. By addressing such concerns early, companies can ensure the safety of their employees and equipment.
IFM’s Cutting-Edge Condition Monitoring Solutions

1. Smart Sensors for Real-Time Data
IFM’s condition monitoring solutions utilize smart sensors that provide real-time, actionable data on the health of electrical equipment. These sensors monitor key parameters such as vibration, temperature, and pressure, providing operators with critical insights that can guide maintenance decisions.
2. Cloud-Based Data Integration
Another key feature of IFM’s condition monitoring systems is the ability to integrate data into cloud-based platforms. This allows businesses to access real-time data from anywhere, at any time. With cloud-based analytics, companies can receive alerts, generate reports, and analyze trends to make informed decisions about their operations.
3. Easy-to-Use Interfaces
IFM understands the importance of user-friendly interfaces, and their condition monitoring systems are designed with ease of use in mind. With intuitive dashboards and straightforward controls, operators can quickly interpret data and take necessary actions. This ease of use helps ensure that even those with limited technical expertise can effectively manage their equipment’s health.
4. Scalability for Diverse Needs
Whether you are running a small electrical operation or managing a large industrial complex, IFM’s condition monitoring solutions are scalable to fit your needs. The modular design allows businesses to add sensors and monitoring tools as their requirements grow, making it an adaptable solution for companies of all sizes.
The Future of Condition Monitoring in the Electrical Industry

Increased Adoption of IoT and AI
As the Internet of Things (IoT) and Artificial Intelligence (AI) continue to reshape the industrial sector, Condition Monitoring is poised to become even more sophisticated. The integration of IoT devices allows for the collection of vast amounts of data, which can then be analyzed using AI algorithms to predict equipment failures with even greater accuracy.
In the future, we can expect more advanced condition monitoring solutions from companies like IFM, where AI-driven insights will lead to even more precise maintenance schedules and further reduce unplanned downtime.
Expansion of Remote Monitoring Capabilities
Remote monitoring is another key trend in the future of Condition Monitoring. With remote access to condition data, operators will be able to monitor equipment from anywhere in the world. This will be especially useful for businesses that operate in multiple locations or have limited on-site personnel.
Integration with Other Industrial Systems
As industrial systems become more interconnected, the role of Condition Monitoring will expand beyond individual equipment. The integration of condition monitoring data with other operational systems, such as energy management or supply chain management, will create a more holistic view of business operations. This level of integration will allow for better decision-making, as businesses can align their maintenance schedules with broader operational strategies.
結論
In conclusion, Condition Monitoring is transforming the way electrical companies approach maintenance and equipment management. By utilizing advanced technologies like smart sensors, cloud-based analytics, and predictive maintenance tools, businesses can improve equipment reliability, reduce costs, and enhance overall performance. As companies like IFM continue to innovate in this field, the future of condition monitoring looks incredibly promising, offering even greater benefits to the electrical industry in terms of efficiency, safety, and productivity.
よくある質問
1. What is Condition Monitoring?
Condition Monitoring is the process of continuously monitoring the health of electrical equipment to detect early signs of failure, allowing for timely maintenance.
2. How can Condition Monitoring reduce downtime?
By detecting potential issues before they result in failure, Condition Monitoring helps schedule maintenance and repairs, preventing unplanned downtime.
3. What are the benefits of Condition Monitoring in the electrical industry?
Key benefits include improved reliability, cost savings through predictive maintenance, increased efficiency, and enhanced safety.
4. Can IFM’s Condition Monitoring solutions be integrated with existing systems?
Yes, IFM’s solutions are scalable and can be easily integrated with existing monitoring systems or cloud platforms.
5. How does Condition Monitoring improve safety?
By tracking parameters such as temperature and pressure, Condition Monitoring can detect risks like overheating, preventing hazardous situations and enhancing safety.