ifm IO-Linkテクノロジーでインダストリー4.0を実現:スマートオートメーションの強化
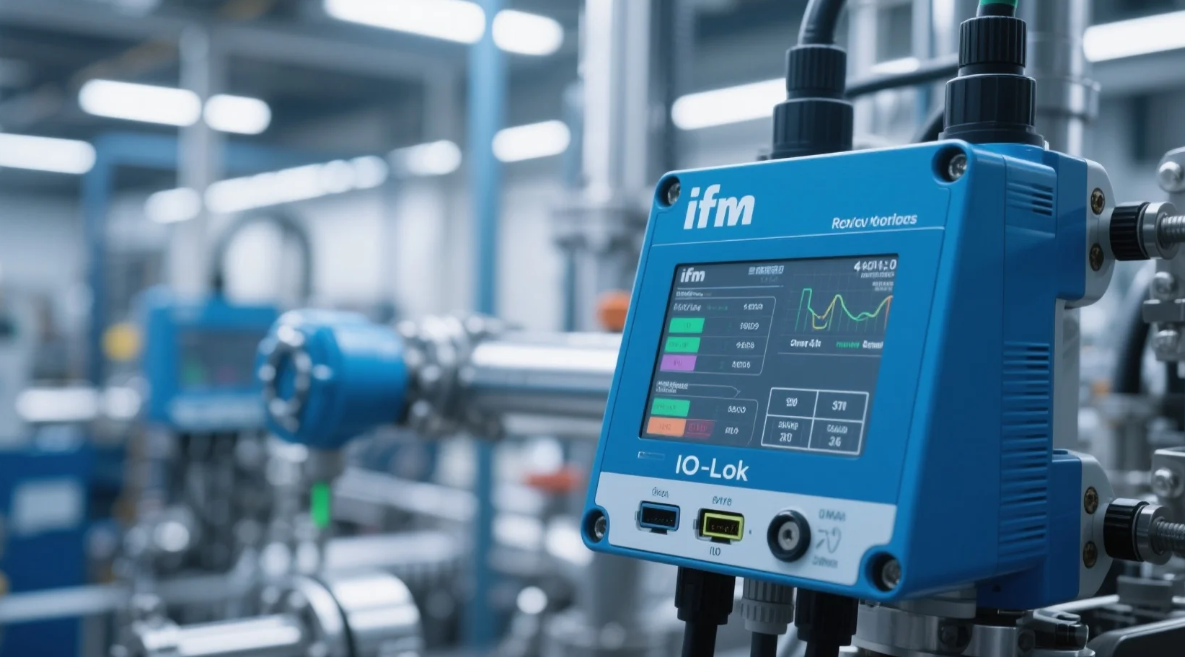
Introduction: Embracing the Smart Future of Automation
In today’s rapidly evolving industrial landscape, ifm IO-Link technology for Industry 4.0 plays a pivotal role in reshaping the future of electrical process control and automation. With the rise of smart manufacturing, companies seek technologies that enable real-time communication, diagnostic capabilities, and easy device integration. ifm’s IO-Link solutions provide precisely that—a standardized interface that bridges the gap between sensors, actuators, and higher-level control systems.
This article explores the benefits, features, and future potential of ifm IO-Link technology for Industry 4.0, offering valuable insights to users in the automation sector.
What is IO-Link and Why It Matters in Industry 4.0?
A Global Standard for Device Communication
IO-Link is an open-standard serial communication protocol (IEC 61131-9) used to connect sensors and actuators to automation systems. Unlike traditional binary I/O, IO-Link allows for bidirectional communication, enabling devices to transmit process data, status updates, and diagnostic information.
The adoption of IO-Link aligns seamlessly with the principles of Industry 4.0, which emphasize connectivity, data accessibility, and autonomous decision-making.
The Role of ifm in Advancing IO-Link Technology
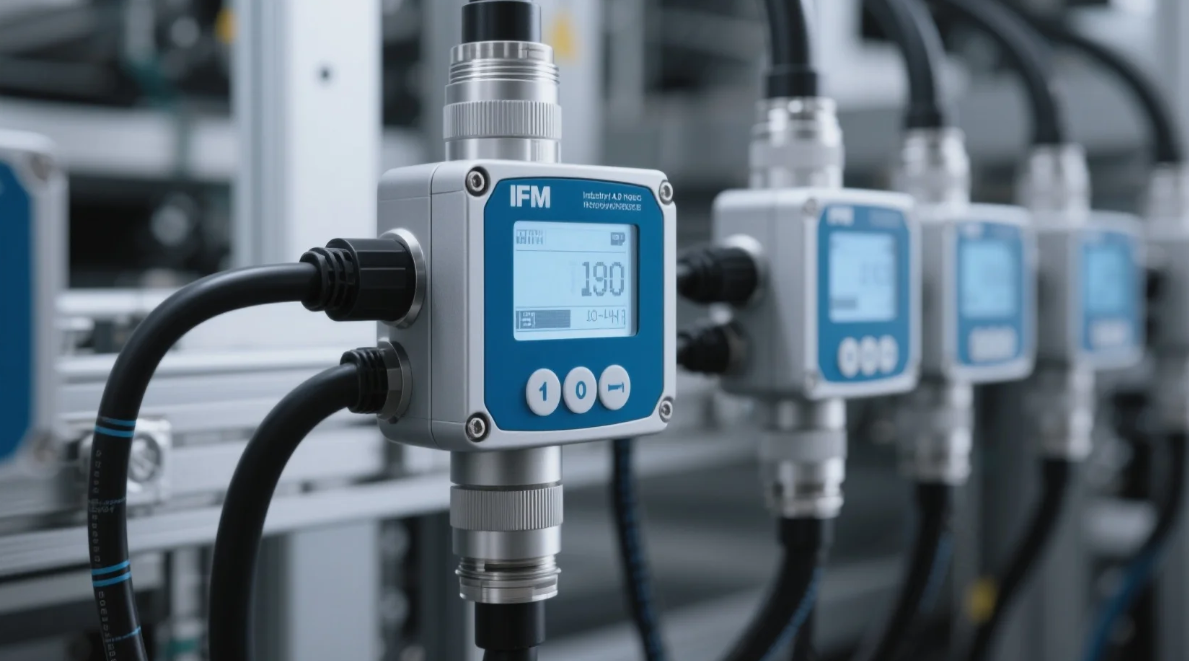
A Trusted Partner in Industrial Automation
ifm electronic, a global leader in sensor and control systems, has been at the forefront of industrial innovation. The company has invested heavily in developing robust IO-Link solutions that deliver performance, reliability, and compatibility across a wide range of industrial environments.
ifm IO-Link technology for Industry 4.0 is characterized by:
- Seamless integration into existing systems
- Real-time data transparency
- Plug-and-play device replacement
- Reduction of downtime via predictive maintenance
These capabilities empower factories to become smarter, more agile, and cost-effective.
Key Benefits of ifm IO-Link Technology for Industry 4.0
1. Enhanced Data Availability
By enabling continuous data exchange, IO-Link helps users access real-time values such as temperature, pressure, or flow. This information allows systems to adapt dynamically, improving efficiency and quality control.
2. Simplified Installation and Commissioning
Traditional analog setups often require extensive wiring and calibration. In contrast, IO-Link uses standard cables and supports automatic parameter setting, reducing engineering time.
3. Predictive Maintenance and Diagnostics
One of the standout features of ifm IO-Link technology for Industry 4.0 is its ability to provide detailed diagnostic data. This predictive insight allows technicians to schedule maintenance before failures occur, minimizing unexpected downtime.
4. Device Standardization and Interoperability
Thanks to its standardized interface, IO-Link devices from ifm can be used across different systems and controllers, improving flexibility and scalability in industrial setups.
Application Areas in Electrical Process Control
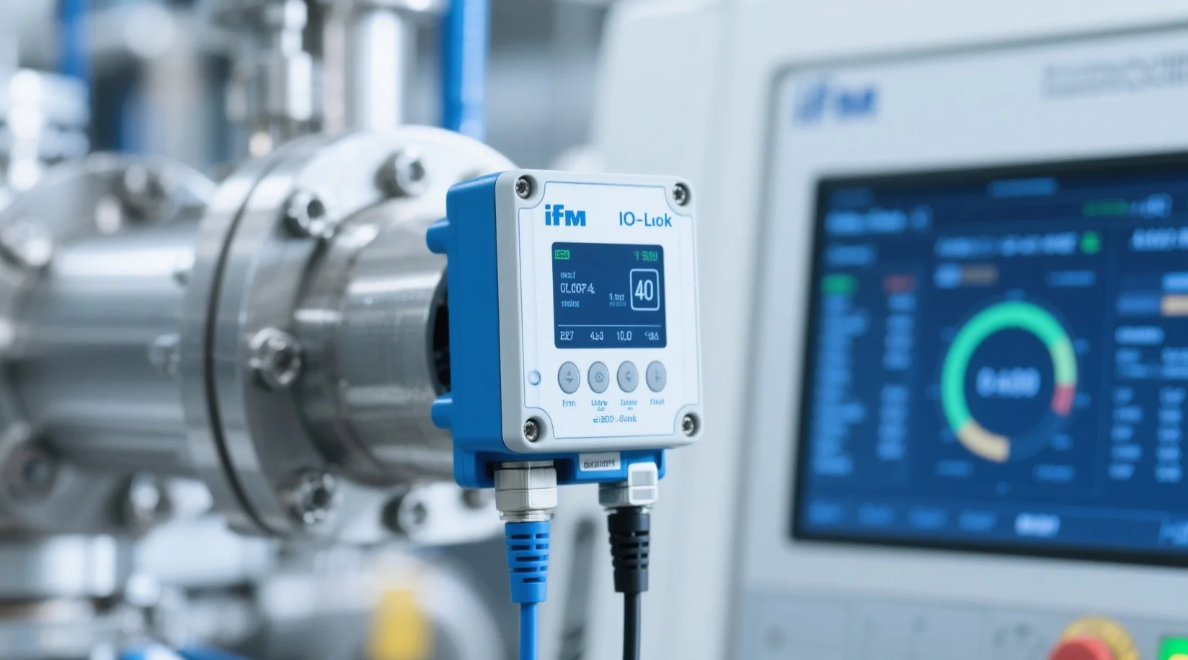
Factory Automation
From conveyor systems to robotic arms, IO-Link sensors ensure every movement is precisely monitored and optimized. They contribute to real-time monitoring, energy efficiency, and fault detection.
Process Industries
In industries such as food and beverage or pharmaceuticals, ifm IO-Link technology for Industry 4.0 ensures hygienic operation, accurate dosing, and compliance with stringent regulatory standards.
Material Handling and Logistics
Smart sensors in logistics systems track item positioning, movement, and environmental conditions. The IO-Link integration facilitates automated warehouse operations and real-time inventory updates.
Challenges and Considerations
While the benefits are substantial, users should be aware of a few challenges:
- IO-Link is limited to point-to-point connections
- Higher initial hardware investment
- Requires compatible IO-Link masters and software tools
Nevertheless, these concerns are generally outweighed by long-term savings, increased uptime, and enhanced flexibility.
Future Outlook: Scaling Smart Manufacturing
を採用した。 ifm IO-Link technology for Industry 4.0 is expected to grow exponentially. As Industry 4.0 principles become more widespread, the need for intelligent, connected devices will only increase. ifm is actively developing newer-generation IO-Link solutions that support advanced analytics, cybersecurity, and even AI integration.
Manufacturers that invest in these technologies now are more likely to stay competitive and resilient in the face of evolving market demands.
Why Choose ifm for IO-Link Integration?
Choosing a reliable partner is critical when transitioning to smart automation. ifm offers:
- Comprehensive product portfolio (sensors, connectors, controllers)
- Global support and training resources
- Long-term commitment to innovation and quality
With its industry-proven expertise and robust support network, ifm stands as a trustworthy ally for digital transformation.
結論
In conclusion, ifm IO-Link technology for Industry 4.0 delivers significant value across diverse sectors of automation and process control. It provides a standardized, reliable, and scalable platform that supports smarter decision-making, reduces costs, and improves overall system performance.
Businesses ready to embrace Industry 4.0 should consider IO-Link solutions from ifm as a strategic step toward building a more connected, intelligent future.
FAQ: ifm IO-Link Technology for Industry 4.0
Q1: What makes ifm IO-Link different from other providers?
A: ifm offers robust hardware, seamless software tools, and a global support ecosystem, ensuring smooth implementation and long-term reliability.
Q2: Is IO-Link backward compatible with existing systems?
A: Yes, IO-Link can be integrated with legacy systems using standard interfaces and IO-Link masters.
Q3: Can IO-Link support real-time control in fast-paced applications?
A: Absolutely. The protocol supports fast cycle times suitable for demanding automation tasks.
Q4: What industries benefit most from ifm IO-Link?
A: Automotive, food processing, pharmaceutical, logistics, and general manufacturing sectors gain substantial efficiency and transparency.
Q5: Is there training available for IO-Link implementation?
A: Yes. ifm provides comprehensive training resources both online and on-site to ensure successful deployment.