Что такое мониторинг состояния в автоматизации?
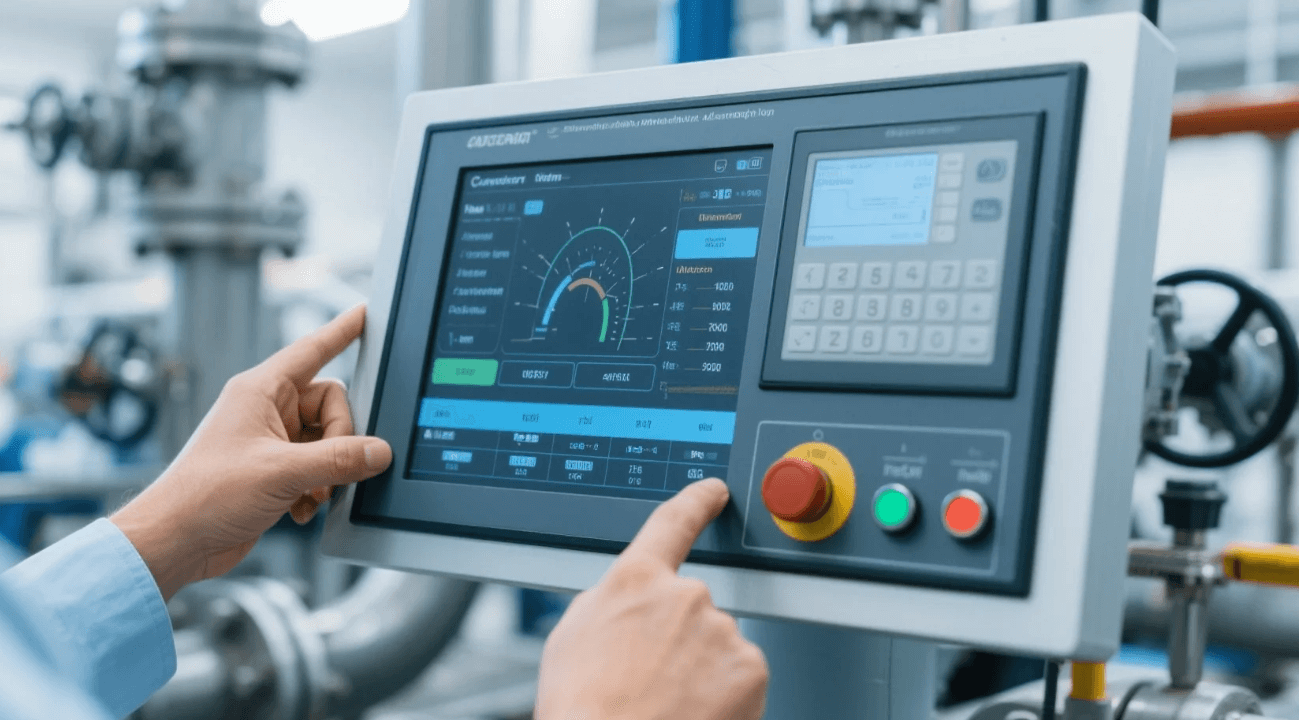
Condition Monitoring in automation refers to the continuous tracking of vital equipment parameters—such as vibration, temperature, and electrical current—to detect early signs of deterioration or failure. In electrical process control systems, this approach ensures optimal performance, prevents unscheduled downtime, and extends asset life by turning raw sensor data into actionable insights.
The Fundamentals of Condition Monitoring
Definition and Core Objectives
- Condition Monitoring is the practice of regularly measuring machine health indicators.
- Its primary goal is to identify anomalies before they evolve into critical failures, thus shifting maintenance strategies from reactive to proactive.
- Key objectives include safety enhancement, cost reduction, and assured production continuity.
Why It Matters in Automation
- In automation, even minor equipment faults can halt entire production lines.
- By embracing Condition Monitoring, engineers gain real-time visibility, enabling timely interventions and minimizing risk.
- The practice aligns with Industry 4.0 principles, leveraging data to optimize processes.
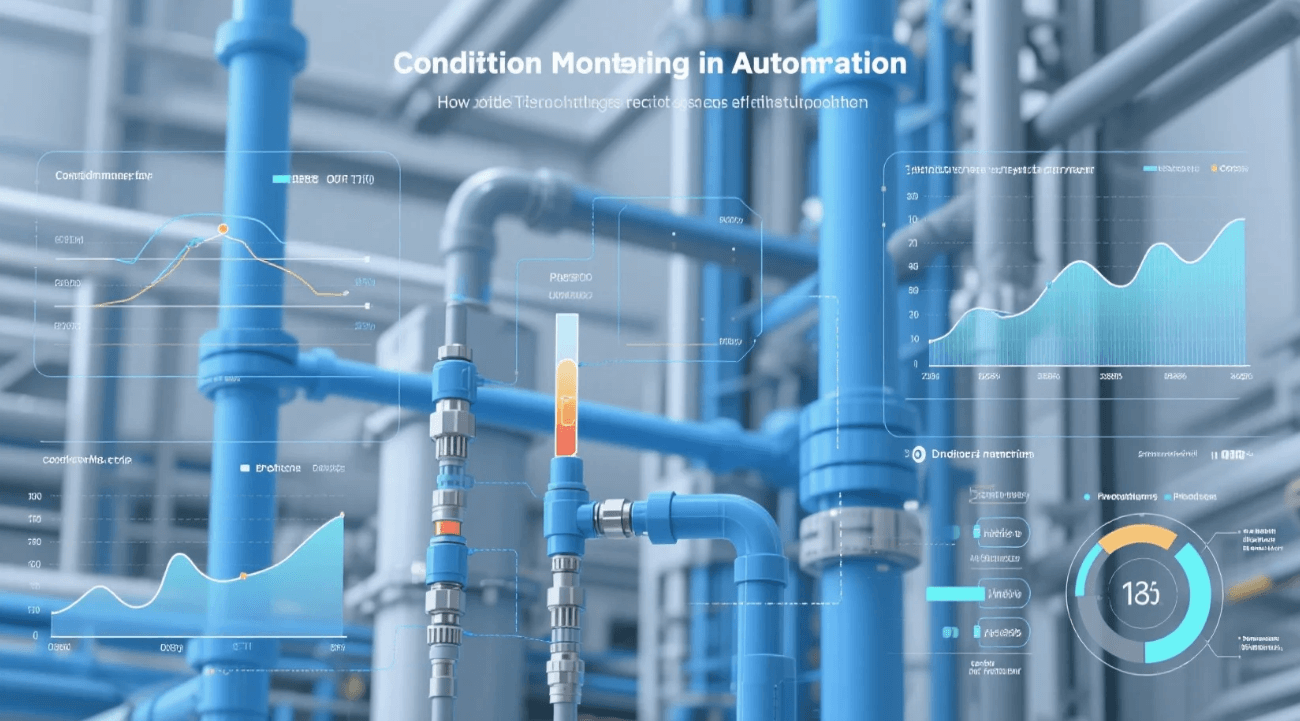
Core Techniques and Technologies
Vibration Analysis
- Widely used for rotating machinery (motors, pumps, fans).
- Sensors capture vibration spectra; deviations from baseline indicate imbalance or bearing wear.
- Data is usually collected via wireless or wired accelerometers.
Thermal Imaging & Temperature Sensing
- Infrared cameras and RTD/thermocouple sensors track heat patterns.
- Hotspots in electrical panels or mechanical joints are flagged for inspection.
- Permits non-contact monitoring in live installations.
Electrical Signature Analysis
- Monitors current and voltage waveforms on motors and drives.
- Changes in harmonic content can reveal rotor bar cracks or winding faults.
- Integration with PLCs allows automated fault detection.
Lubricant and Wear-Debris Analysis
- Oil samples are examined for contaminant particles and viscosity changes.
- Detects gear wear, contamination, and fluid degradation over time.
- Especially valuable in hydraulic systems and gearboxes.
Ultrasonic Testing
- High-frequency sound waves detect leaks, partial discharges, and bearing issues.
- Handheld or permanently mounted ultrasonic sensors are employed.
- Early leak detection in pneumatic lines prevents energy loss.
How Condition Monitoring Works
Sensor Deployment and Data Collection
- Sensors are mounted at critical points (bearings, electrical panels, gearboxes).
- Data is transmitted to edge devices or gateways, then relayed to SCADA or IIoT platforms.
Baseline Establishment
- Initial healthy-state data is recorded to serve as a reference point.
- Statistical thresholds are defined around these baselines to trigger alerts.
Real-Time Analysis and Alerting
- Data analytics modules compare live inputs against thresholds.
- When anomalies exceed limits, alerts are dispatched via email, SMS, or dashboard notifications.
Trending and Predictive Insights
- Historical data trends are analyzed to forecast remaining useful life (RUL).
- Predictive maintenance schedules are generated based on these forecasts.
Benefits of Condition Monitoring in Process Control
Reduced Downtime and Maintenance Costs
- Early fault detection prevents catastrophic failures and unplanned stops.
- Maintenance is scheduled only when needed, reducing labor and parts expenses.
Extended Equipment Lifespan
- Addressing issues at inception stops accelerated wear, preserving asset integrity.
- Investments in capital equipment yield higher returns.
Enhanced Safety and Compliance
- Monitoring electrical panels for overheating and partial discharge ensures worker safety.
- Many industries mandate condition monitoring to meet regulatory standards.
Data-Driven Decision Making
- Real-time KPIs on machine health inform operational and strategic planning.
- Production schedules can be adjusted proactively based on equipment forecasts.
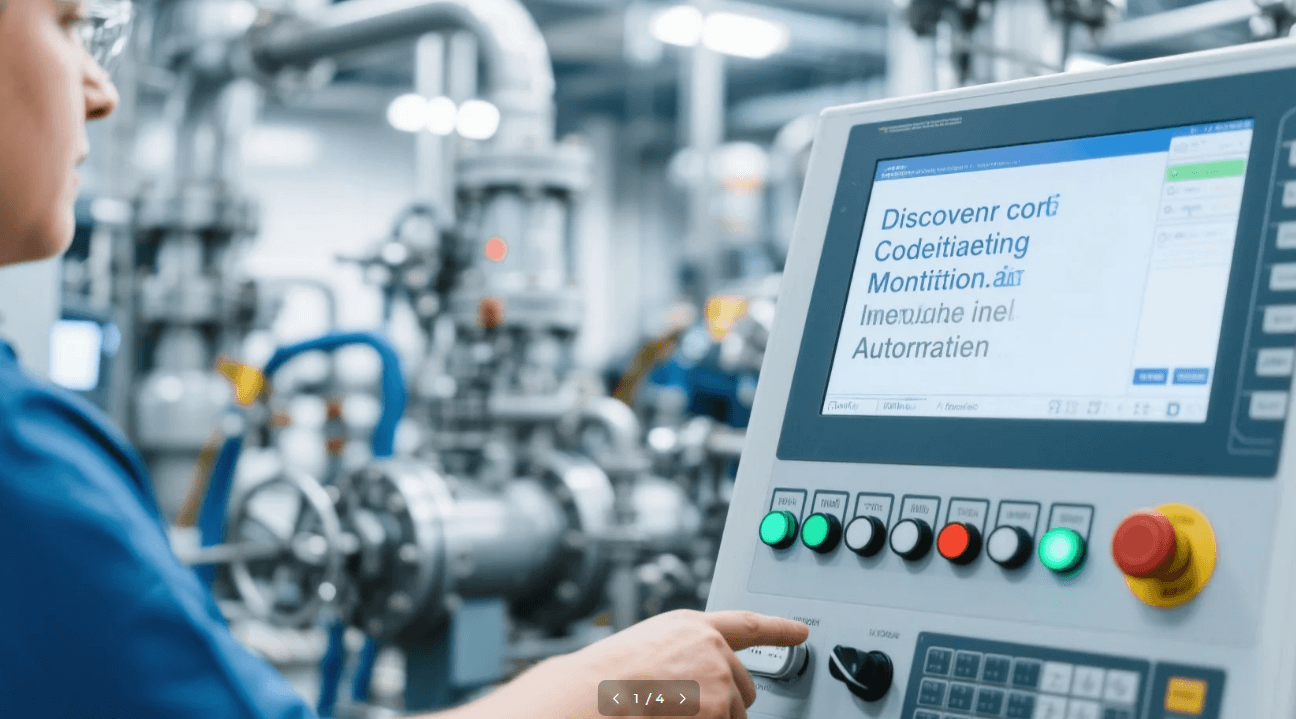
Integrating Condition Monitoring into Automation Architecture
Connection to PLCs and SCADA
- Condition data is fed into PLC logic or SCADA alarms.
- This permits automated process adjustments—such as speed reduction or shutdown—when a fault is detected.
IIoT Platforms and Cloud Analytics
- Edge gateways preprocess data, sending selected metrics to cloud dashboards.
- Advanced analytics, ML models, and digital twins live in these platforms, delivering deep insights.
Interoperability and Standards
- Protocols like OPC UA, Modbus TCP, and MQTT ensure seamless data exchange.
- ISO 13372 and ISO 14224 define terminology and data structures for consistency.
Deployment Best Practices
Asset Prioritization
- Use a risk-based approach to rank equipment by criticality and failure impact.
- Begin monitoring on high-value, high-risk assets for fastest ROI.
Phased Rollout Strategy
- Pilot on a single production line or facility zone.
- Refine sensor placements, threshold settings, and alert logic before enterprise-wide adoption.
Cross-Functional Team Engagement
- Involve maintenance, operations, and IT stakeholders from the start.
- Training programs ensure end-users understand dashboards, alerts, and response protocols.
Continuous Program Evaluation
- Conduct quarterly reviews of analytics accuracy, false-positive rates, and downtime metrics.
- Adjust baselines and thresholds based on real-world performance.
Case Study Highlight: Automated Pump Station
- Context: A chemical plant’s pump stations suffered unplanned shutdowns every quarter.
- Solution: Installed vibration and temperature sensors, integrated via Modbus into the plant’s DCS.
- Outcome: Early detection of bearing misalignment cut downtime by 60% and reduced bearing replacement costs by 40%.
Overcoming Common Challenges
- Data Overload: Apply edge computing to filter raw data, sending only key features upstream.
- Legacy Equipment: Use clamp-on or portable sensors to monitor machines without rewiring.
- Skill Gaps: Partner with technology vendors for training and knowledge transfer workshops.
- Budget Constraints: Demonstrate quick wins on pilot projects to secure further funding.
The Future of Condition Monitoring
AI-Driven Anomaly Detection
- Deep learning models will sense subtle patterns missed by classical thresholding.
- Self-learning systems will refine baselines automatically.
Digital Twin Integration
- Virtual replicas of assets will simulate failure modes, validating maintenance plans.
- Digital twins and real-time sensor streams will converge for holistic asset health views.
Edge-to-Cloud Orchestration
- More analytics will occur at the asset edge for instant responses.
- Summarized data will feed cloud platforms for enterprise-level insights.
ЧАСТО ЗАДАВАЕМЫЕ ВОПРОСЫ
Q1: What types of failures can Condition Monitoring detect?
Common faults include bearing wear, imbalance, misalignment, electrical winding issues, leaks, and overtemperature events.
Q2: How much ROI can be expected?
Enterprises typically see a 20–40% reduction in maintenance costs and 30–50% less unplanned downtime within the first year.
Q3: Is it suitable for small plants?
Yes—modular, pay-as-you-go sensor networks and cloud analytics make it cost-effective for facilities of any size.
Q4: How often should data be analyzed?
Critical assets warrant continuous real-time monitoring; less critical machines can be checked periodically (e.g., hourly or daily).
Заключение
In today’s automated facilities, Condition Monitoring serves as the linchpin of proactive maintenance. By deploying targeted sensors, integrating data with control systems, and applying advanced analytics, organizations achieve safer, more reliable operations and maximize equipment value. Embracing this paradigm shift not only prevents failures but also unlocks the full potential of electrical process control and automation. Let me know if you’d like a tailored deployment plan, sensor recommendations, or analytics platform comparisons!